Traditional hinges may seem like a small component in the vast world of industrial manufacturing, but they hold a significant position in the sector. Their pivotal role, pun intended, can be observed in countless applications across various industries.
Traditional hinges are those basic mechanical bearings which connect two solid objects, allowing for a limited angle of rotation between them.
The introduction of modern designs and materials might overshadow the importance of these traditional tools, but their ubiquity in industrial manufacturing proves their time-tested reliability and efficiency. Now, let’s dive into various aspects of these traditional hinges, expanding our understanding of their significance.
The Origin and History of Traditional Hinges
Traditional hinges have ancient roots. Historical records and archaeological findings suggest their use in ancient civilizations like Egypt and Rome.
Their design might have been basic, but it solved a primary concern of the time: creating a pivot for doors, gates, and other objects. These early designs laid the foundation for what would become a mainstay in industrial manufacturing.
Materials Commonly Used
Brass, iron, and steel – these are some of the conventional materials used to create traditional hinges. Each material has its unique properties that offer varying levels of strength, corrosion resistance, and weight.
Durable materials ensure that the hinges can withstand the pressure of frequent use, especially in industrial settings where resilience and longevity are paramount.
Different Types of Traditional Hinges
In industrial manufacturing, the type of hinge used is crucial for the product’s functionality. Butterfly, strap, and continuous are some of the common traditional hinge types.
While their applications might differ, their primary purpose remains the same: to provide a pivot point. Selecting the right type ensures seamless operation and longevity of the assembly.
Traditional Hinge Manufacturing Process
Creating traditional hinges involves several stages. The process starts with choosing the right material, followed by shaping, bending, and sometimes, welding.
Once the desired shape is achieved, these hinges undergo treatments like galvanization or powder coating to enhance durability. This rigorous process ensures that they meet the required industrial standards.
Benefits in Industrial Manufacturing
While they might seem simple, traditional hinges offer various benefits in industrial manufacturing. Their simplicity is a boon, leading to easy installation and maintenance.
Furthermore, their robust design ensures they can handle heavy loads and stresses, making them suitable for various industrial applications, from machinery doors to heavy-duty containers.
Maintenance and Lifespan
In the industrial sector, longevity and reliability are critical. With proper maintenance, traditional hinges can last a long time, offering consistent performance throughout.
Regular inspections for wear and tear, lubricating the pivot points, and ensuring they’re free from rust can significantly extend their lifespan, ensuring unhindered operations in an industrial setting.

Potential Issues and Solutions
Like all mechanical components, traditional hinges aren’t free from issues. Regular usage can lead to wear, causing squeaking noises or decreased efficiency.
Addressing these problems timely through lubrication, replacement of worn parts, or adjusting alignment ensures that the hinges continue to function optimally, minimizing potential downtime in industrial operations.
Innovations in Traditional Hinge Design
Even in the realm of traditional hinges, innovation isn’t stagnant. Engineers continuously strive to enhance their design, incorporating features that boost their efficiency and lifespan.
From introducing self-lubricating materials to improving the overall design for better weight distribution, these innovations ensure that the hinges remain relevant in today’s advanced industrial landscape.
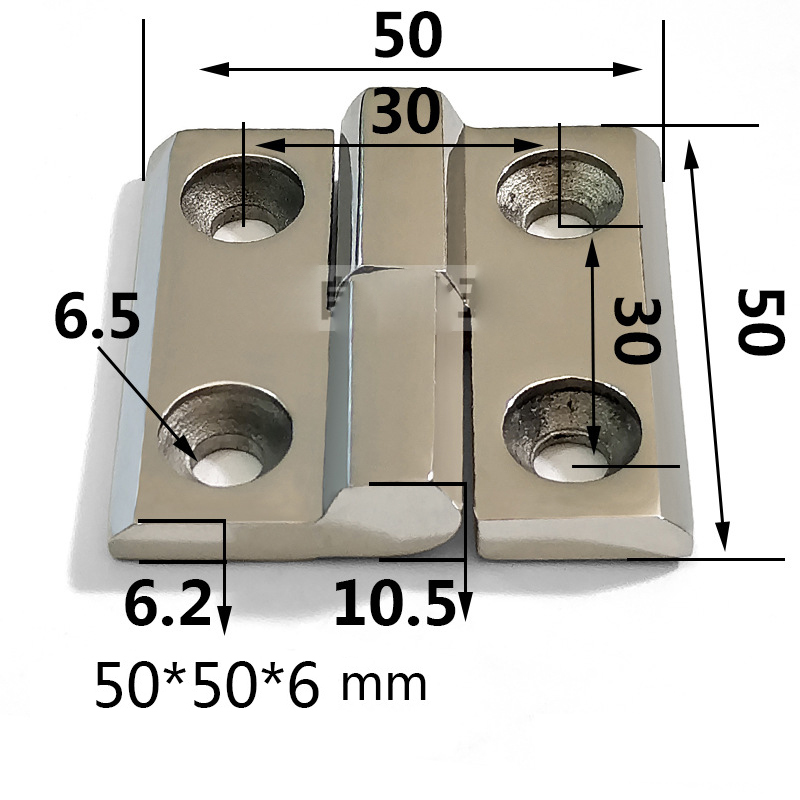
Conclusion
Traditional hinges, with their historical significance and continued relevance, stand as a testament to their robustness and reliability. Their pivotal role in industrial manufacturing is undeniably crucial. As the sector evolves, these hinges, rooted in tradition, continue to pivot towards the future with grace.
You might also be interested: