Ever thought about how the hinges, the unsung heroes in the industrial manufacturing world, are held together? We often overlook their importance, but I assure you, their role is far from minor.
Hinges are held together through a combination of precision-engineered components and materials. They employ a simple yet effective assembly that involves pins, knuckles, and leaves. Intrigued? Let’s delve into the details.
Stay with me, as we journey into the fascinating world of industrial hinge assembly, exploring each component, its function, and the meticulous processes involved in their manufacture.
How are the components of a hinge made?
In the heart of a hinge, there are three main components: the pin, the knuckle, and the leaf. What’s their magic? They ensure the hinge’s robust and fluid movement.
Firstly, the pin, a long cylindrical component, sits at the center of the hinge. It’s usually made of hardened steel for durability and smooth operation. Manufacturing processes such as turning and grinding ensure precise dimensions and high-quality surface finishes.
Then, we have the knuckle, the hollow section that accommodates the pin. Knuckles are usually formed through a process called cold rolling, where the material is passed through rollers under high pressure. This gives the knuckle its round shape and the necessary strength.
How are the components assembled?
After the components are manufactured, they need to be assembled. So, how do these parts fit together to make a complete hinge?
The assembly process begins with the leaves. These are the flat parts of the hinge, which attach to the moving object and the stationary framework. The leaves have half-knuckles that align with each other when the leaves are parallel.
The half-knuckles are then interlocked to form a full knuckle, and the pin is inserted through them. This creates the pivot point for the hinge, allowing it to open and close smoothly.
How is the pin secured in place?
Now that we know how the pin fits into the knuckles, let’s discuss how it’s kept securely in place. How does this process work, and why is it important?
The pin is typically secured by a retaining ring or a bend at one end of the pin. These prevent the pin from slipping out during operation. In some designs, the pin might be welded into place for added security.
Securing the pin is a crucial step in hinge assembly. It ensures that the hinge operates smoothly and reliably over its lifetime, withstanding the rigors of industrial applications.
What types of materials are used for hinges?
Hinges are made from various materials to cater to diverse industrial needs. But what are these materials, and why are they chosen?
Stainless steel is a popular choice for many hinges due to its corrosion resistance, durability, and strength. For more demanding applications, materials like brass or bronze might be used due to their higher resistance to wear and heat.
How does the choice of material affect the hinge?
The choice of material plays a significant role in the hinge’s performance and durability. But, how does the material influence these factors?
Materials with higher resistance to wear and heat ensure the hinge’s longevity in demanding environments. On the other hand, materials like stainless steel offer excellent corrosion resistance, making them ideal for applications exposed to harsh weather conditions or corrosive substances.
What are the most common types of industrial hinges?
With numerous industrial applications, different types of hinges are required to meet specific needs. What are these types, and where are they used?
Butt hinges and continuous hinges are commonly used due to their strength and versatility. They can be found in various applications, from heavy machinery doors to industrial cabinets.
Pivot hinges, on the other hand, are used when the hinge must be hidden, such as for aesthetic reasons or to prevent tampering. These are commonly seen in secure enclosures or machinery guards.
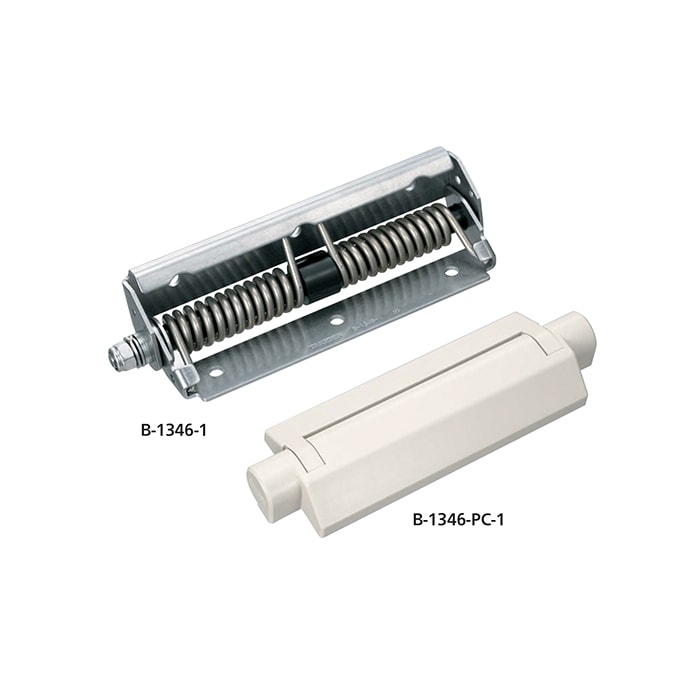
Conclusion
By exploring the intricacies of industrial hinges, we’ve unveiled the meticulous processes involved in their manufacturing. From the careful creation of each component to the precise assembly, every step contributes to the hinge’s functionality and durability. Regardless of the sector, it’s clear that the humble hinge is an essential player in the industrial world.
You might also be interested: